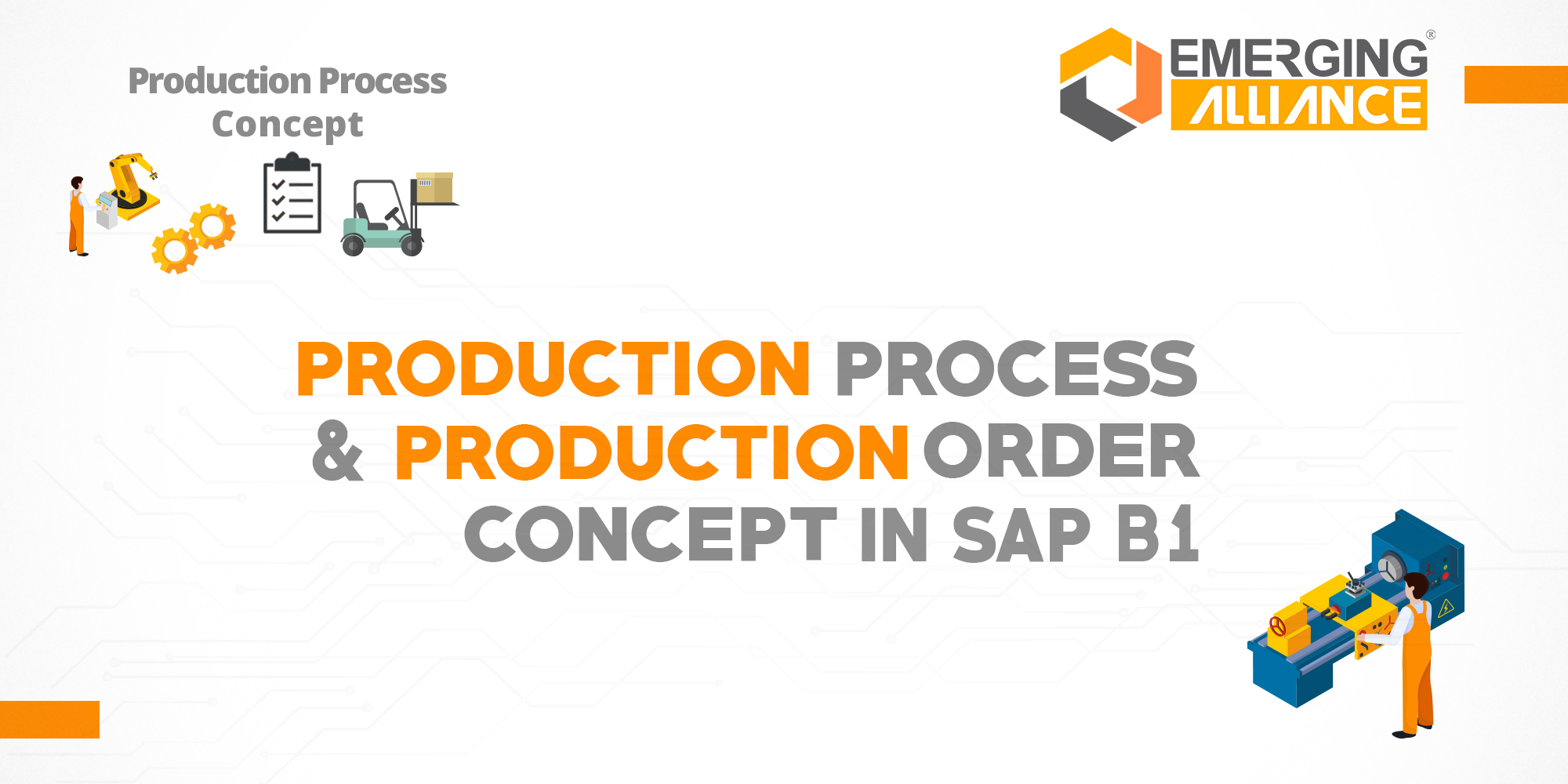
PRODUCTION PROCESS AND PRODUCTION ORDER CONCEPT IN SAP BUSINESS ONE
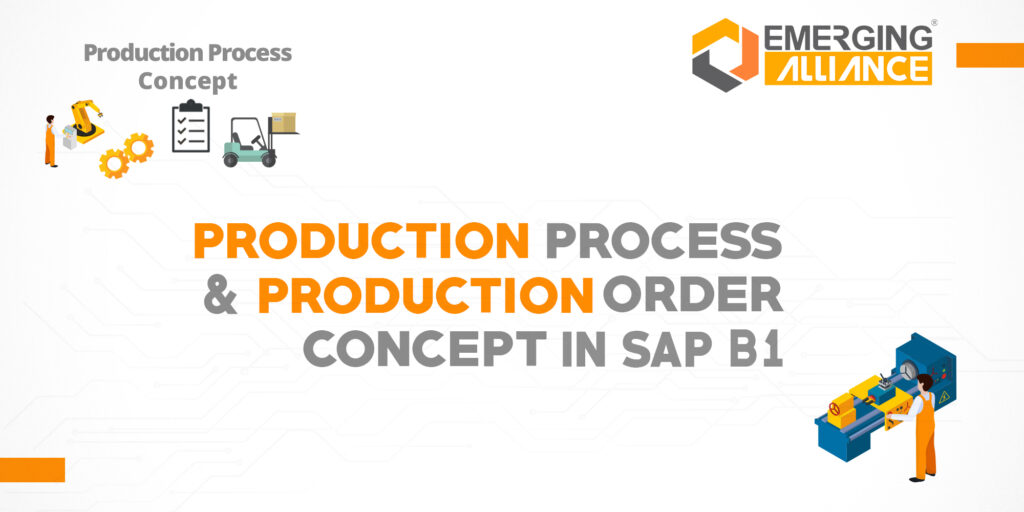
Important Steps in Production Execution:
In SAP Business One, The production process starts with creating a Production Order. This is the main document in the production process. It records the progress of the production process for each item produced.
Before the work begin, Production Order status must be changed from “planned” to “Released”. At this point, the Production Order can begin collecting the costs of production.
Components used in the production process can be released to the shop floor (depending on the issuing method).
When all work is done, you should report completion of the production order. At this point, the finished items are received in the warehouse.
Note that when the automatic method for issuing components to the shop floor is selected, the components and resources are reported as issued as soon as you choose report completion.
When the production process is over, the Production Order is closed. This closure creates a journal entry for balancing inventory accounts at perpetual inventory-managed companies.
A Production Order is a command to produce (or repair) a production item.
A Bill of Material (BOM) is copied into the Production Order document. Then the needed quantity of finished item is entered together with the desired due date of production and other relevant data.
The Production Order also tracks all the material transactions and costs that are involved in the production process.
Note that production orders can be generated in the MRP, Pick and Pack and Production processes as well.
Get started today.
Visit: www.emerging-alliance.com
Pingback: Sap Business One Changing A Route Sequence In A Production Order
Pingback: Competition Feature Of The CRM Module | EA Blog