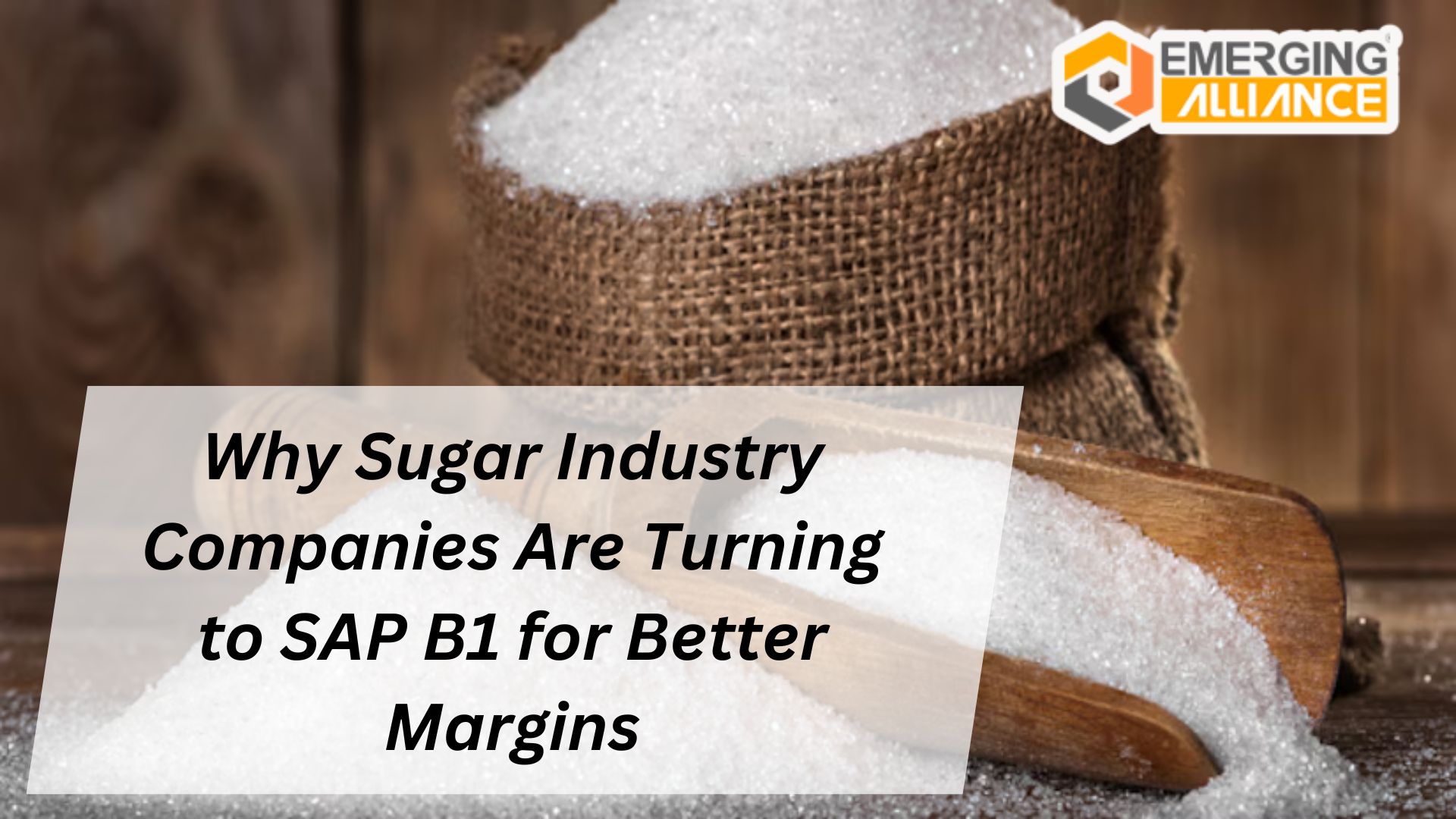
Why Sugar Industry Companies Are Turning to SAP B1 for Better Margins
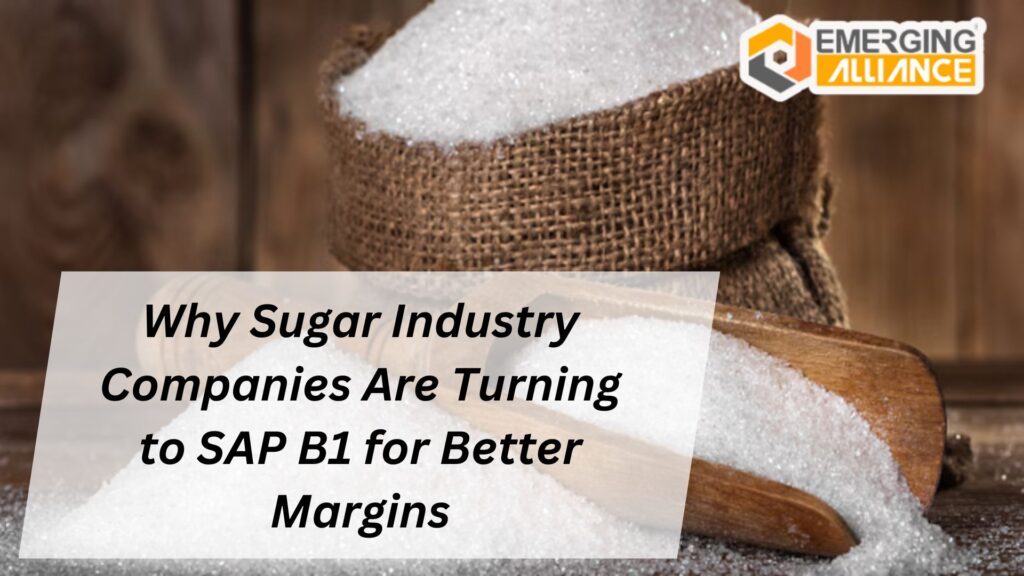
SAP B1 for Sugar Manufacturers: Key to Efficient Operations and Higher Profits
The sugar industry is highly competitive and constantly challenged by fluctuating market prices, rising production costs, and complex supply chain management. To remain profitable and gain a competitive edge, companies in the sugar industry are increasingly turning to SAP Business One (SAP B1) for streamlined operations and better financial margins. In this blog, we’ll explore why SAP B1 is becoming the preferred choice for sugar manufacturers and how it helps improve overall efficiency and profitability.
Challenges in the Sugar Industry
The sugar industry faces multiple challenges that directly affect profitability and operational efficiency:
- Volatile Market Prices: Unstable sugar prices create uncertainty in revenue and profit margins.
- High Production Costs: Rising costs of raw materials, labor, and machinery increase production expenses.
- Complex Supply Chain: Managing supply chain logistics, from sourcing raw materials to delivering finished products, is a critical challenge.
- Regulatory Compliance: Meeting government regulations and quality standards requires efficient data tracking and reporting.
- Inventory Management: Overproduction or underproduction can lead to financial losses and missed market opportunities.
How SAP Business One Solves Key Issues in Sugar Industry
1. Enhanced Supply Chain Management
SAP Business One offers real-time visibility into the supply chain, allowing sugar manufacturers to track and optimize each stage of production. With better demand forecasting and inventory management, companies can reduce wastage and ensure timely delivery.
2. Cost Control and Financial Insights
SAP B1 integrates financial data with operational processes, giving sugar manufacturers a complete view of production costs and profit margins. This helps in identifying areas where expenses can be reduced and resources can be better allocated.
3. Automated Compliance and Reporting
SAP Business One for the sugar industry helps automate compliance processes, ensuring that companies meet industry regulations without manual intervention. Custom reports and dashboards provide quick access to key performance indicators (KPIs) and audit trails.
4. Production Efficiency and Quality Control
SAP B1 enables real-time monitoring of production processes, ensuring that quality standards are maintained. It allows sugar manufacturers to quickly identify and resolve production bottlenecks, reducing downtime and improving overall efficiency.
5. Inventory and Raw Material Management
SAP solutions for the sugar industry enable precise tracking of raw materials and finished products. This ensures optimal inventory levels and reduces the risk of overproduction or stockouts, improving working capital and reducing storage costs.
Why Sugar Companies Are Choosing SAP B1
- Scalable and Flexible: SAP Business One is scalable to meet the growing needs of sugar manufacturers, from small businesses to large-scale producers.
- Industry-Specific Customization: SAP B1 can be customized to meet the specific requirements of the sugar industry, including handling seasonal demand changes and market price fluctuations.
- User-Friendly Interface: SAP B1’s intuitive interface ensures quick adoption and ease of use for employees across departments.
- Improved Decision-Making: With real-time data and integrated financial insights, sugar manufacturers can make informed decisions to increase profitability and reduce operational costs.
FAQs: Boosting Sugar Industry Margins with SAP B1
What is SAP Business One (SAP B1)?
SAP Business One is an integrated enterprise resource planning (ERP) solution designed to help small and medium-sized businesses manage their operations, including finance, production, and supply chain.
Why is SAP B1 suitable for the sugar industry?
SAP B1 helps sugar manufacturers manage production costs, supply chain logistics, and financial data in one platform, improving efficiency and profitability.
How does SAP B1 help reduce production costs in the sugar industry?
SAP B1 tracks production expenses, identifies cost-saving opportunities, and helps optimize resource allocation.
Can SAP B1 handle supply chain challenges in the sugar industry?
Yes, SAP B1 provides real-time supply chain visibility, improving inventory management and reducing delivery delays.
How does SAP B1 improve financial margins in sugar manufacturing?
SAP B1 integrates financial data with operational processes, helping manufacturers monitor costs and improve profit margins.
Does SAP B1 help with regulatory compliance in the sugar industry?
Yes, SAP B1 automates compliance reporting and ensures that sugar manufacturers meet industry standards.
Can SAP B1 improve product quality in sugar manufacturing?
Yes, SAP B1 tracks production processes and quality control, ensuring consistent product standards.
Is SAP Business One scalable for growing sugar businesses?
Yes, SAP B1 is highly scalable, making it suitable for both small and large sugar manufacturers.
How does SAP B1 improve decision-making for sugar manufacturers?
SAP B1 provides real-time insights and performance reports, enabling better business decisions.
What are the key benefits of using SAP B1 for sugar manufacturers?
The key benefits include cost reduction, improved supply chain efficiency, enhanced quality control, better financial insights, and increased profitability.
SAP Business One for the sugar industry is transforming how manufacturers manage production, supply chains, and financial operations. By integrating all business processes into a single platform, SAP B1 helps sugar companies achieve better profit margins, improve production efficiency, and maintain a competitive edge in the market.
If you’re ready to take your sugar manufacturing business to the next level, consider implementing SAP Business One today and experience the benefits of enhanced efficiency and profitability.