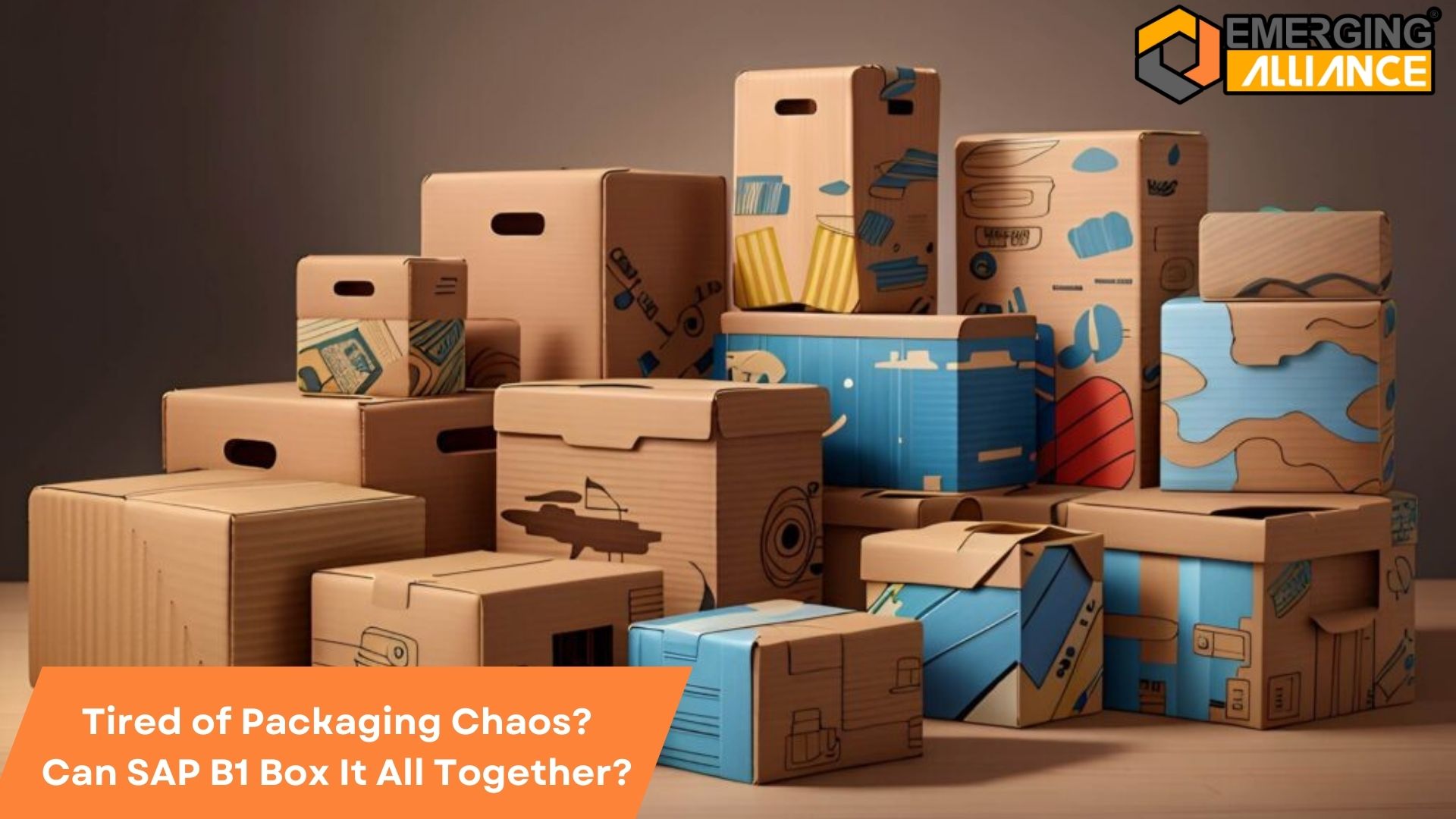
Tired of Packaging Chaos? Can SAP B1 Box It All Together?
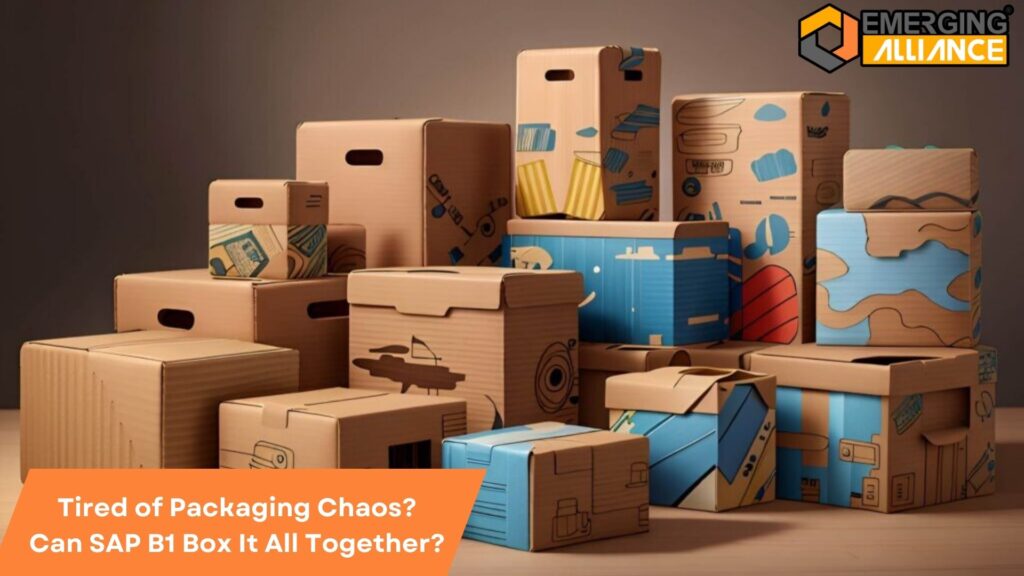
Unwrapping Success: How SAP B1 is Revolutionizing the Packaging Industry
The packaging industry is evolving at a rapid pace. With increasing consumer demand, complex supply chains, and rising production costs, businesses in the packaging sector face immense pressure to streamline operations, minimize waste, and enhance customer satisfaction. Traditional systems and fragmented processes are no longer enough to keep up with the pace of modern business.
Enter SAP B1 (SAP Business One) — a comprehensive ERP (Enterprise Resource Planning) solution designed specifically for small and medium-sized businesses. For the packaging industry, SAP B1 offers a unified platform to manage inventory, automate production, control costs, and boost customer satisfaction — all while simplifying complex operations.
But can SAP B1 truly box it all together and deliver a seamless solution for the packaging industry? Let’s unwrap the answers.
Why the Packaging Industry is Facing Operational Chaos
The packaging industry sits at the crossroads of manufacturing and logistics. Unlike other industries, it deals with a wide variety of materials (plastic, paper, glass, metal), varying product sizes, and intricate customer requirements. This complexity creates significant challenges:
➡️ Material Shortages: Unpredictable supply chain disruptions lead to inconsistent material availability.
➡️ Production Inefficiencies: Delays, machine breakdowns, and inconsistent production cycles disrupt order fulfillment.
➡️ High Operational Costs: Inefficient use of materials, energy, and labor inflates production costs.
➡️ Poor Inventory Management: Overstocking or understocking raw materials results in either high storage costs or production delays.
➡️ Customer Dissatisfaction: Missed deadlines and order errors affect customer retention and brand reputation.
SAP B1 addresses these challenges with a unified platform that automates key processes, enhances visibility, and enables real-time decision-making.
How SAP B1 Streamlines the Packaging Industry
1. Smart Inventory Management — No More Stockouts or Overstocking
Managing inventory is one of the biggest challenges in the packaging industry due to the wide variety of materials involved — from plastics, paper, and cardboard to metals and specialty coatings. Many packaging companies face stock shortages or overstocking, both of which lead to significant financial losses and operational inefficiencies.
SAP B1 offers an advanced inventory management module that provides real-time tracking and automated replenishment, ensuring that you always have the right materials on hand without holding excess stock.
🔎 Automated Replenishment: SAP B1 generates automatic purchase orders when stock levels drop below a specified threshold, preventing production delays caused by material shortages.
🔎 Warehouse Optimization: SAP B1 allows you to organize and categorize materials efficiently within warehouses, reducing picking times and improving inventory accuracy.
🔎 Stock Visibility: The system provides complete visibility over inventory levels across multiple locations, helping you avoid duplication and stockouts.
🔎 FIFO and LIFO Tracking: SAP B1 supports both FIFO (First-In-First-Out) and LIFO (Last-In-First-Out) inventory tracking, ensuring accurate cost calculations and better inventory turnover.
For instance, a packaging company using SAP B1 was able to reduce inventory holding costs by 18% within six months by automating stock replenishment and optimizing warehouse organization.
2. Streamlined Production Scheduling — Boost Output Without Wasted Effort
Production in the packaging industry involves a complex set of steps — cutting, printing, folding, laminating, gluing, and packaging — all of which need to be precisely timed and coordinated. Delays at any stage can disrupt the entire production cycle, resulting in missed deadlines and increased costs.
SAP B1 helps simplify and automate production planning by providing real-time insights into machine performance, labor availability, and order deadlines.
✅ Automated Work Orders: SAP B1 generates automated work orders based on sales data, reducing the time it takes to initiate production.
✅ Machine Integration: SAP B1 integrates with existing production machinery, allowing you to monitor machine uptime and performance.
✅ Capacity Planning: The system helps identify production bottlenecks and enables you to adjust schedules dynamically to meet order deadlines.
✅ Resource Allocation: SAP B1 allocates resources (materials, labor, and machine capacity) based on order priority and deadlines.
For example, a leading packaging manufacturer reduced production lead times by 25% using SAP B1’s automated scheduling and capacity planning features.
3. Cost Control and Profitability — Manage Margins Like a Pro
Profit margins in the packaging industry are tight due to high material costs and competitive pricing pressures. Many businesses struggle to accurately track production costs and identify areas for savings.
SAP B1 provides a comprehensive financial management module that enables businesses to monitor costs in real-time and make data-driven decisions to improve profitability.
💡 Real-Time Cost Analysis: SAP B1 breaks down costs into material, labor, and overhead categories, allowing you to pinpoint areas of inefficiency.
💡 Waste Reduction: The system identifies wasteful production practices and suggests corrective measures.
💡 Budgeting and Forecasting: SAP B1 provides detailed budgeting and forecasting tools to help you manage expenses and anticipate future costs.
💡 Automated Financial Reporting: Generate profit and loss statements, balance sheets, and cash flow reports with a single click.
One packaging company increased its profit margins by 12% within a year of implementing SAP B1’s cost management and financial tracking capabilities.
4. Real-Time Order Management — On-Time, Every Time
In the packaging industry, customer satisfaction hinges on accurate order fulfillment and timely delivery. Late deliveries or incorrect orders can damage customer relationships and result in lost business.
SAP B1 centralizes order management, allowing you to track orders from the moment they are placed to the time they are delivered.
🚚 Order Tracking: SAP B1 provides real-time order tracking, enabling customers to check the status of their orders.
🚚 Automated Picking and Packing: The system automates order picking and packing, reducing the chances of human error.
🚚 Shipping Integration: SAP B1 integrates with major shipping carriers, allowing you to generate shipping labels and track deliveries.
🚚 Customer Portal: Provide customers with access to an online portal where they can place, modify, and track their orders.
A packaging company that switched to SAP B1 reduced order processing errors by 40% and increased on-time deliveries by 30% within the first six months.
5. Quality Control and Regulatory Compliance
The packaging industry is subject to stringent quality and safety regulations. Defective or non-compliant packaging can lead to product recalls, fines, and damaged brand reputation.
SAP B1 automates quality control processes, ensuring that products meet both customer expectations and regulatory requirements.
✔️ Inline Quality Checks: Perform real-time quality checks at each stage of production.
✔️ ISO and GMP Compliance: SAP B1 helps maintain compliance with industry standards like ISO and GMP.
✔️ Lot and Batch Tracking: The system tracks materials and finished products by lot and batch, ensuring traceability in case of product recalls.
✔️ Non-Conformance Reporting: Generate reports for non-conforming products and initiate corrective action.
One packaging company reduced product defects by 35% after implementing SAP B1’s automated quality control and compliance tracking features.
6. Customer Relationship Management (CRM) — Build Loyalty, Not Just Sales
The packaging industry is highly competitive, and customer loyalty plays a crucial role in long-term success. SAP B1 includes an integrated CRM that allows businesses to manage customer interactions and order histories from a single platform.
👥 Order Customization: Offer personalized packaging options based on customer preferences.
👥 Automated Follow-Ups: Set up automated follow-ups for repeat orders or special promotions.
👥 Complaint Resolution: Track and resolve customer complaints quickly.
👥 Customer Insights: Generate reports on customer buying behavior and trends.
A packaging company that implemented SAP B1’s CRM module increased customer retention by 22% within a year.
7. Forecasting and Demand Planning — Stay Ahead of Market Trends
Packaging businesses often struggle with demand fluctuations caused by seasonal changes, market trends, and customer preferences. SAP B1 provides advanced forecasting tools to help you anticipate demand and adjust production schedules accordingly.
📊 Predictive Analytics: SAP B1 analyzes historical data to forecast future demand.
📊 Seasonal Adjustments: Adjust production capacity and staffing based on seasonal trends.
📊 Minimized Stockouts: By anticipating demand, you can maintain optimal stock levels without overproduction.
A packaging company using SAP B1’s forecasting tools reduced stockouts by 50% and improved order fulfillment rates.
8. Supply Chain Integration — Synchronize Operations from Start to Finish
Managing suppliers, manufacturers, and logistics partners is complex and time-sensitive. SAP B1 integrates all aspects of the supply chain into a single platform, ensuring smooth communication and coordination.
🔄 Supplier Performance Monitoring: Evaluate supplier performance based on delivery timelines and product quality.
🔄 Automated Procurement: Automatically generate purchase orders based on stock levels.
🔄 Delivery Tracking: Track shipments and provide real-time updates to customers.
9. Business Intelligence and Reporting — Make Data-Driven Decisions
SAP B1 comes with built-in business intelligence tools that provide real-time insights into business performance.
📊 Custom Dashboards: Create customized dashboards to monitor KPIs and track performance.
📊 Data Visualization: Generate charts and graphs to identify trends and patterns.
📊 Performance Tracking: Monitor department and employee performance to identify improvement areas.
10. Scalability and Expansion — Grow Without Growing Pains
As your packaging business expands, you need a system that grows with you. SAP B1 is highly scalable, allowing you to add new modules and functionalities as needed.
🚀 Multi-Location Management: Manage multiple production facilities from a single platform.
🚀 Add-On Compatibility: Integrate third-party add-ons for industry-specific features.
🚀 Flexible Licensing: Scale user access and licenses based on business growth.
A packaging company that expanded operations to five new locations was able to centralize management using SAP B1 without increasing administrative overhead.
Why SAP B1 is the Complete Solution for Packaging Businesses
From inventory management and production scheduling to customer service and financial tracking, SAP B1 addresses every aspect of the packaging industry’s operational needs. Its scalability, real-time data capabilities, and automation features make it the ideal solution for packaging businesses seeking to improve efficiency and profitability.
FAQs
1. How does SAP B1 improve material traceability in the packaging industry?
SAP B1 provides batch and serial number tracking, ensuring full visibility over raw materials and finished products.
2. Can SAP B1 handle seasonal demand fluctuations in the packaging industry?
Yes, SAP B1 includes advanced forecasting tools to adjust production schedules based on seasonal demand.
3. How does SAP B1 improve supplier management for packaging companies?
SAP B1 monitors supplier performance, automates procurement, and ensures timely delivery of materials.
4. What cost-saving opportunities does SAP B1 offer to packaging businesses?
SAP B1 identifies material wastage, labor inefficiencies, and production bottlenecks to reduce costs.
5. Can SAP B1 manage custom packaging orders?
Yes, SAP B1 allows you to create and track custom orders with specific customer requirements.
6. How does SAP B1 enhance quality control in packaging?
SAP B1 automates quality checks and maintains compliance records for audits.
7. Does SAP B1 integrate with existing production machinery?
Yes, SAP B1 can integrate with most manufacturing and packaging machinery for real-time data sharing.
8. Can SAP B1 automate billing and invoicing for packaging companies?
Yes, SAP B1 automates billing, invoicing, and financial reporting.
9. How does SAP B1 improve customer satisfaction in the packaging industry?
SAP B1 provides real-time order tracking, accurate delivery estimates, and proactive customer service.
10. How does SAP B1 help packaging companies scale their operations?
SAP B1’s modular structure allows businesses to add new features and expand functionality as they grow.