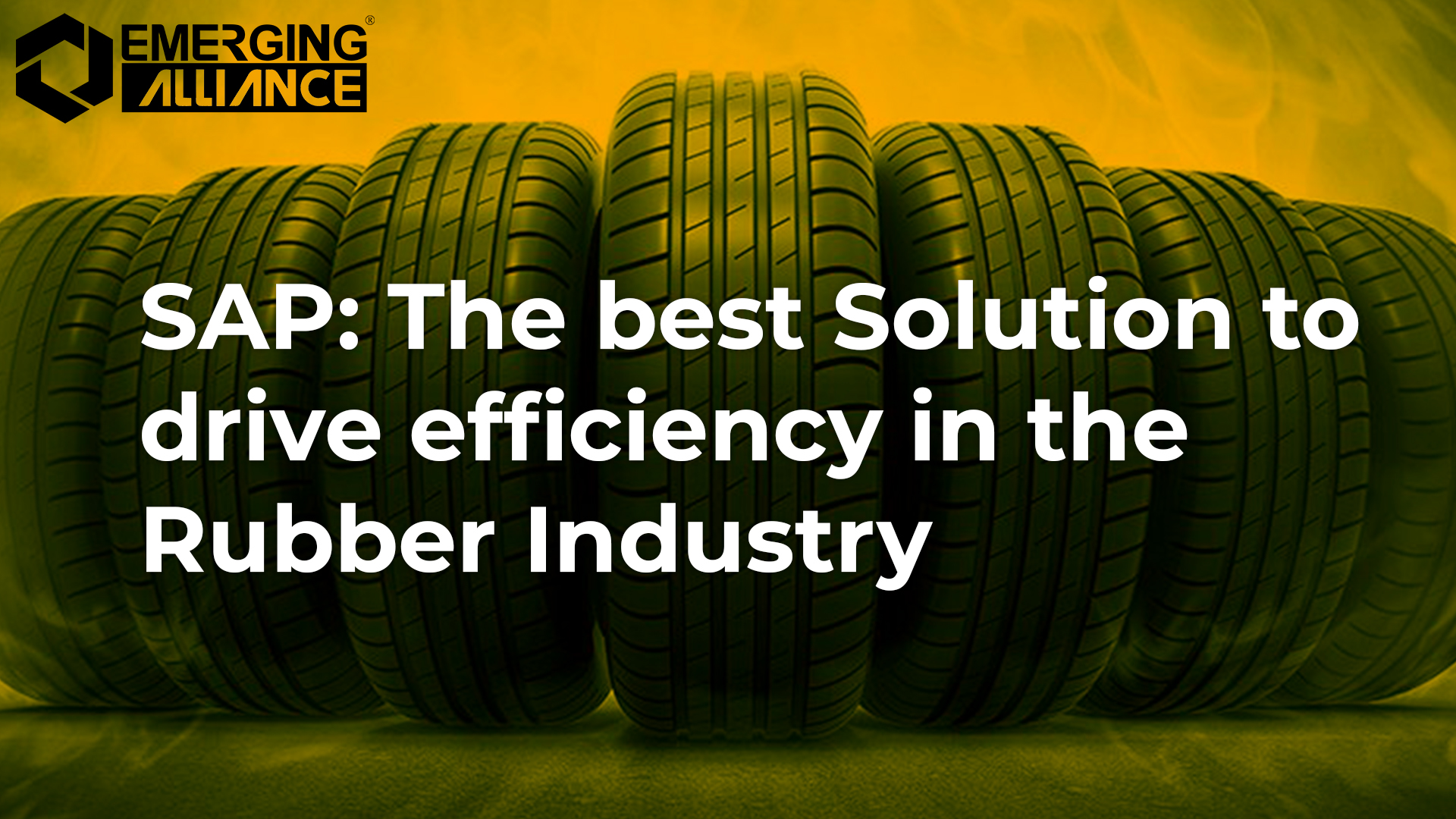
SAP: The best Solution to drive efficiency in the Rubber Industry
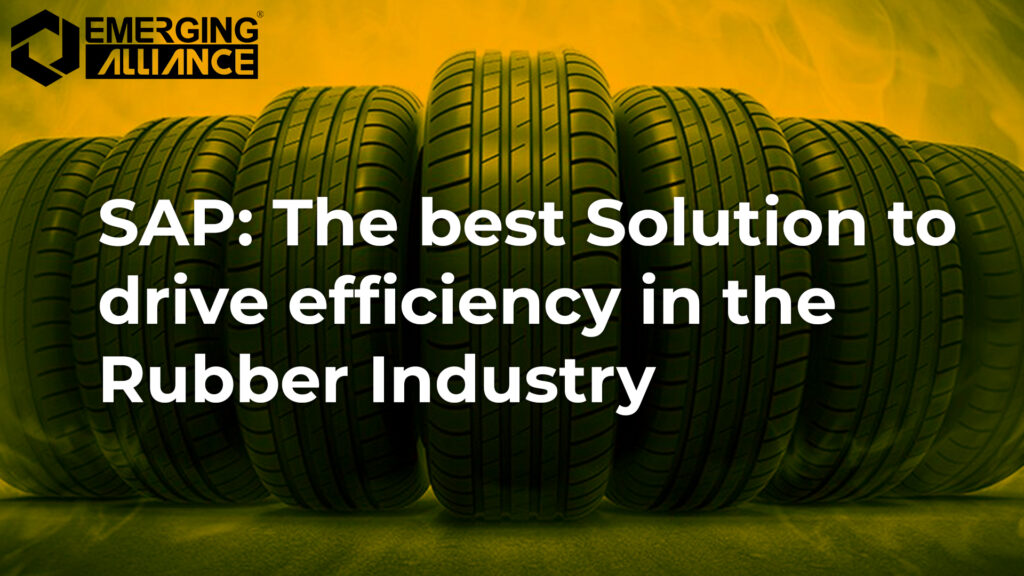
SAP for Rubber Industry | Rubber Industry SAP
In the fast-paced and highly competitive rubber industry, maintaining efficient operations, ensuring product quality, and effectively managing the supply chain are crucial for success. To meet these challenges head-on, many rubber manufacturers turn to SAP (Systems, Applications, and Products) as their go-to enterprise resource planning (ERP) solution. SAP offers a comprehensive suite of modules tailored to the specific needs of the rubber industry, empowering companies to streamline processes, optimize resource allocation, and enhance overall productivity.
In this article, we will delve into the key features within SAP that play a vital role in the rubber industry. From material management and production planning to quality control, sales, and financial management, we will explore how SAP enables rubber manufacturers to achieve operational excellence while ensuring adherence to quality standards and meeting customer demands. By harnessing the power of SAP, rubber industry players can drive efficiency, gain better control over their processes, and ultimately strengthen their competitive edge in the market.
Here’s a detailed overview of some features in SAP (Systems, Applications, and Products) that are commonly used in the rubber industry:
Material Management (MM):
Master Data Management:
SAP MM allows you to define and manage various master data elements such as raw materials, finished products, suppliers, and vendors specific to the rubber industry.
Purchase Management:
Streamline procurement processes by automating purchase requisitions, purchase orders, and goods receipt processes. This ensures efficient inventory management and timely availability of rubber materials.
Inventory Control:
SAP MM provides tools for inventory planning, stock monitoring, and replenishment strategies to optimize rubber material stocks, reduce wastage, and avoid shortages.
Production Planning (PP):
Bill of Materials (BOM):
Define the hierarchical structure of rubber products and their components within SAP. BOMs enable efficient production planning, including material requirements planning (MRP) and capacity planning.
Routing:
Specify the sequence of operations required to manufacture rubber products. Routing functionality helps optimize production flows, resource allocation, and scheduling to improve overall production efficiency.
Shop Floor Control:
Monitor and track the progress of rubber production orders in real-time, ensuring timely completion, efficient resource utilization, and adherence to production schedules.
Quality Management (QM) in SAP for Rubber Industry:
Inspection Planning:
Create inspection plans to define quality control points and quality characteristics specific to rubber industry requirements. These plans ensure that rubber materials and finished products meet quality standards.
Quality Notifications:
Record and manage quality-related issues or non-conformities during the production process or during product inspection. This feature helps in identifying, tracking, and resolving quality issues promptly.
Statistical Process Control (SPC):
SAP QM includes tools for statistical analysis of rubber production processes, such as control charts and process capability analysis. SPC helps monitor process stability, identify variations, and implement corrective actions.
Sales and Distribution (SD) in SAP for Rubber Industry:
Customer Order Management:
Capture customer orders, create sales contracts, and manage pricing conditions for rubber products. SAP SD enables efficient order processing, including order confirmation, delivery, and invoicing.
Shipping and Transportation:
Plan and execute the shipment of rubber products, including managing transportation schedules, route optimization, and tracking deliveries. This feature ensures timely and accurate delivery to customers.
Pricing and Rebates:
Define pricing conditions, discounts, and rebates for rubber products based on customer contracts or pricing agreements. SAP SD allows flexible pricing structures to accommodate the specific needs of the rubber industry.
Financial Accounting (FI) and Controlling (CO) in SAP:
Cost Accounting:
SAP FI-CO provides cost allocation mechanisms to track production costs associated with rubber manufacturing processes. This includes capturing direct material costs, labor costs, overheads, and calculating product costs.
Financial Reporting:
Generate financial reports, including profit and loss statements, balance sheets, and cash flow statements, to gain insights into the financial performance of rubber-related operations.
Cost Center Accounting:
Allocate costs to specific cost centers within the rubber industry, enabling cost analysis, budgeting, and variance reporting.
These are just a few of the many SAP features that can be leveraged by the rubber industry. SAP offers a comprehensive suite of modules that can be tailored to meet the specific needs of rubber manufacturers, facilitating efficient operations, improved quality control, streamlined supply chain management, and enhanced financial visibility.
To know more about SAP services, visit us at: https://emerging-alliance.net/