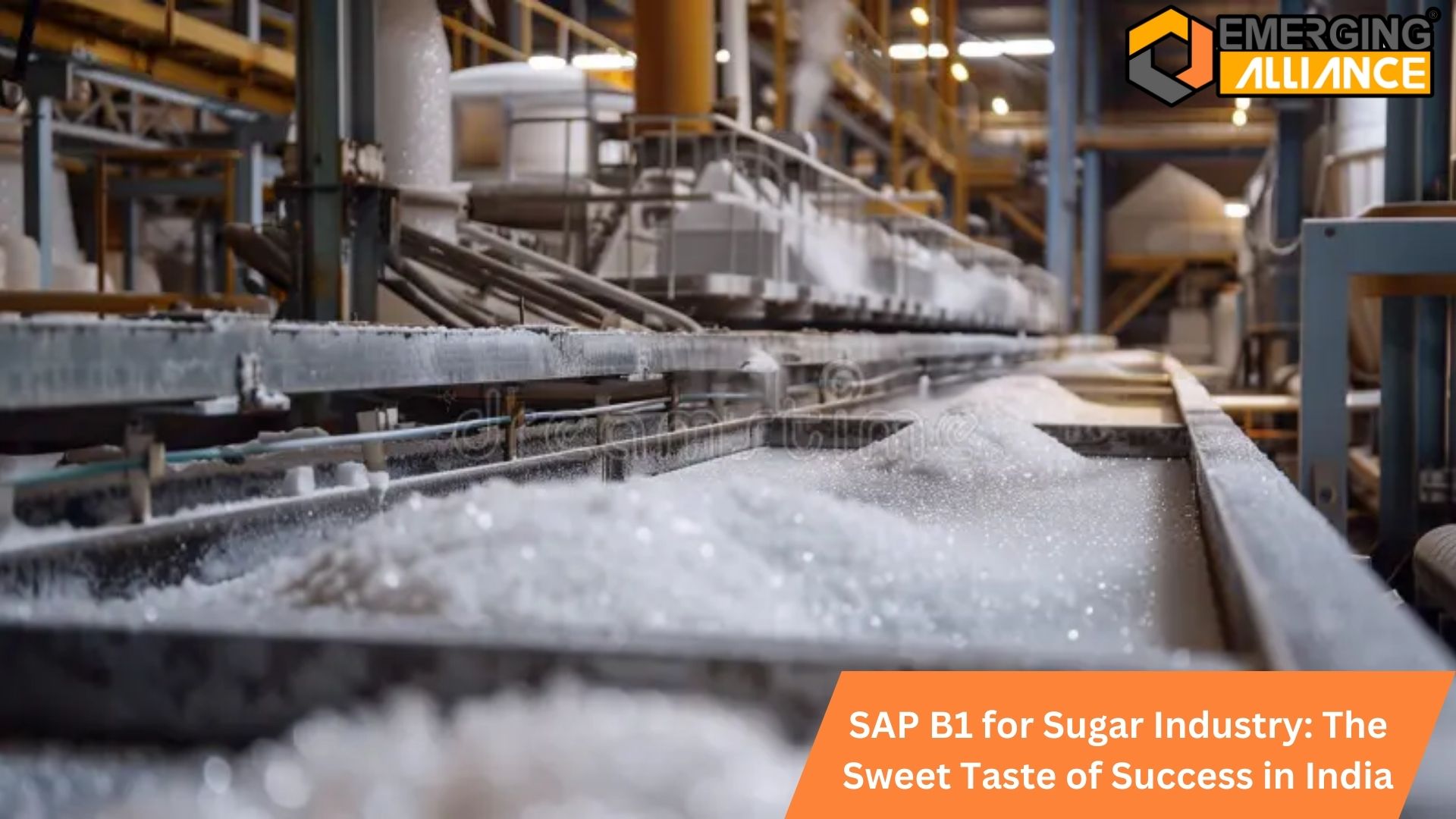
SAP B1 for Sugar Industry: The Sweet Taste of Success in India
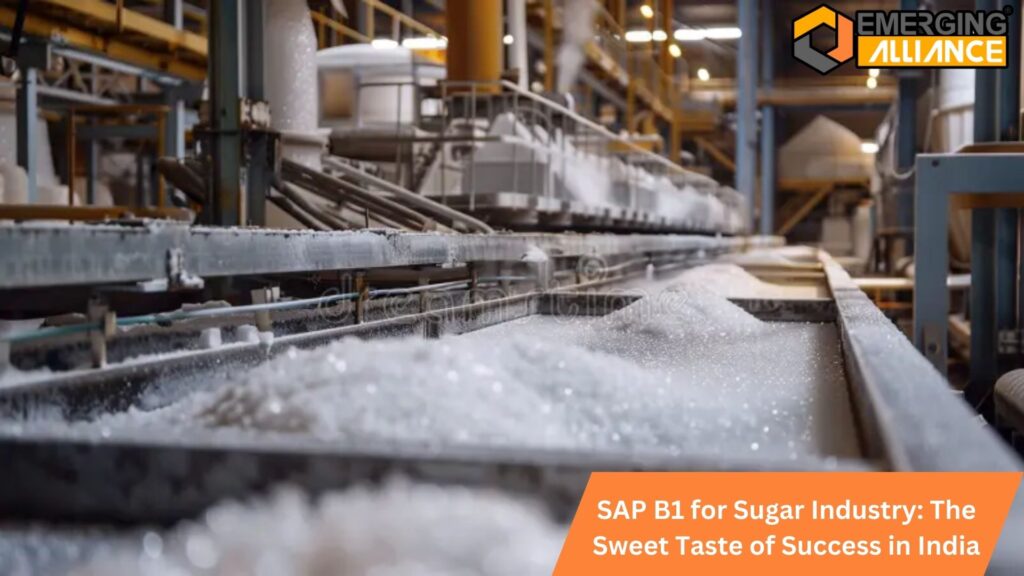
How SAP B1 is Stirring Sweet Success for India’s Sugar Industry
The sugar industry in India is one of the largest contributors to the country’s agricultural and manufacturing sectors. India is the second-largest producer of sugar globally, with over 530 operational sugar mills producing approximately 30 million tons of sugar annually. Despite its massive scale, the industry faces persistent challenges — from supply chain inefficiencies and fluctuating raw material prices to production bottlenecks and compliance issues.
Enter SAP B1 (SAP Business One) — a comprehensive ERP solution tailored to address the specific needs of the sugar industry. With its powerful features for managing procurement, production, inventory, and finance, SAP B1 enables sugar manufacturers to automate processes, improve decision-making, and boost profitability.
In this blog, we’ll explore how SAP B1 is transforming the sugar industry in India, making operations smoother, smarter, and more profitable.
Challenges Facing the Sugar Industry in India
Despite its global standing, the sugar industry in India grapples with several complex issues:
🚨 1. Fluctuating Raw Material Costs
Sugarcane prices are heavily influenced by government policies, weather conditions, and market demand. When prices rise, manufacturers face increased production costs, which squeeze profit margins.
🚨 2. Supply Chain Inefficiencies
The sugar production process involves multiple stages — from sugarcane farming and crushing to refining and distribution. Delays or mismanagement at any stage can disrupt the entire supply chain.
🚨 3. Compliance and Regulatory Pressure
The sugar industry is subject to strict government regulations and quality standards. Failing to meet compliance requirements can result in penalties and reputational damage.
🚨 4. Seasonal and Regional Variability
Sugar production is heavily dependent on the monsoon season. Regional differences in soil quality and climate further complicate production planning and resource allocation.
🚨 5. Quality Control and Waste Management
Maintaining consistent sugar quality is essential to meet customer expectations and avoid wastage during processing. Inefficient quality control can lead to higher rejection rates and financial losses.
How SAP B1 Solves These Challenges
1. Optimized Raw Material Procurement and Cost Control
SAP B1 integrates real-time market data and procurement scheduling to help sugar manufacturers manage fluctuating sugarcane prices. Manufacturers can set procurement rules based on cost thresholds and production needs.
✅ Example: A sugar mill in Maharashtra reduced its raw material costs by 12% after adopting SAP B1’s automated procurement module.
2. Streamlined Production and Resource Allocation
SAP B1 allows sugar manufacturers to automate production scheduling, ensuring efficient use of equipment, labor, and materials. Real-time monitoring of production lines reduces downtime and improves output.
✅ Example: A sugar refinery in Tamil Nadu increased production efficiency by 18% within six months of implementing SAP B1.
3. Enhanced Inventory Management and Batch Tracking
SAP B1 provides a centralized inventory system that tracks raw materials, semi-finished goods, and finished products. Batch-level tracking ensures traceability and compliance with industry standards.
✅ Example: A sugar factory in Gujarat reduced wastage by 22% using SAP B1’s inventory management tools.
4. Improved Quality Control and Product Consistency
SAP B1 enables sugar manufacturers to set up quality control checkpoints throughout the production process. Automatic alerts notify managers of quality issues, ensuring timely corrective action.
✅ Example: A sugar mill in Uttar Pradesh reduced product rejection rates by 14% using SAP B1’s quality management module.
5. Real-Time Financial Insights and Cost Management
SAP B1 offers robust financial tools to monitor expenses, forecast budgets, and analyze profitability. Automated financial reporting ensures accurate tax calculations and compliance.
✅ Example: A sugar manufacturer in Karnataka improved profit margins by 10% through better cost control and financial reporting with SAP B1.
6. Smarter Supply Chain Management
SAP B1 helps sugar manufacturers manage the entire supply chain — from sugarcane sourcing to finished product delivery. Real-time logistics tracking and automated order processing improve delivery efficiency.
✅ Example: A sugar producer in Punjab reduced delivery delays by 30% after integrating SAP B1’s supply chain management module.
Why the Sugar Industry in India Needs SAP B1
The Indian sugar industry operates in a highly dynamic environment where small operational improvements can lead to significant financial gains. SAP B1 offers a scalable solution that addresses industry-specific challenges, enabling sugar manufacturers to increase productivity, reduce costs, and maintain product consistency.
🔥 Key Benefits of SAP B1 for Sugar Industry:
✅ Increased production efficiency through automation and resource optimization
✅ Improved financial management and cost tracking
✅ Better compliance with local and global regulatory standards
✅ Enhanced product quality and customer satisfaction
✅ Real-time data insights for informed decision-making
✅ Reduced operational bottlenecks and production downtime
Implementation of SAP B1 in Sugar Industry
Phase 1: Business Assessment and Requirement Analysis
- Analyze current production, supply chain, and financial workflows
- Identify operational gaps and bottlenecks
Phase 2: Customization and Integration
- Customize SAP B1 modules to align with sugar production needs
- Integrate with existing machinery and third-party systems
Phase 3: Data Migration and Training
- Transfer historical data to SAP B1
- Provide hands-on training to staff
Phase 4: Testing and Rollout
- Conduct pilot testing to identify potential issues
- Gradually roll out SAP B1 across all production units
Future of SAP B1 in the Sugar Industry
As the Indian sugar industry grows, manufacturers will face increased pressure to improve efficiency, reduce environmental impact, and meet evolving consumer demands. SAP B1 is positioned to support this transition by providing innovative solutions for digital transformation and smart manufacturing.
Emerging trends such as AI-driven production optimization and blockchain-based supply chain tracking can be integrated with SAP B1 to unlock even greater value for sugar manufacturers.
The sugar industry in India is at a pivotal moment where technological innovation can drive significant competitive advantages. SAP B1 offers sugar manufacturers a comprehensive solution to streamline operations, enhance product quality, and boost profitability. By adopting SAP B1, India’s sugar mills can transform their operations and achieve sustainable growth in an increasingly competitive market.
FAQs
1. How does SAP B1 help manage fluctuating sugarcane prices?
SAP B1 provides real-time market insights and automated procurement tools to adjust pricing and purchasing strategies dynamically.
2. Can SAP B1 reduce wastage in sugar production?
Yes, SAP B1 optimizes inventory and batch tracking to minimize wastage and improve production efficiency.
3. How does SAP B1 improve financial reporting in the sugar industry?
SAP B1 automates financial reporting, ensuring accurate tracking of costs, revenues, and profit margins.
4. Can SAP B1 handle large-scale production in sugar mills?
Yes, SAP B1 is scalable and can handle complex production processes and large volumes of data.
5. Does SAP B1 offer real-time inventory tracking?
Yes, SAP B1 provides real-time inventory updates and batch-level tracking.
6. How does SAP B1 improve supply chain efficiency?
SAP B1 offers real-time tracking, order processing automation, and logistics management to reduce delays.
7. Can SAP B1 enhance product quality in the sugar industry?
Yes, SAP B1 provides quality control checkpoints to maintain consistent product standards.
8. How does SAP B1 help with compliance in the sugar industry?
SAP B1 automates compliance reporting and ensures adherence to industry regulations.
9. Is SAP B1 suitable for small and medium-sized sugar manufacturers?
Yes, SAP B1 is designed for scalability and can support both small and large production units.
10. How long does it take to implement SAP B1 in a sugar manufacturing unit?
Implementation typically takes 3 to 6 months, depending on the complexity of the business.