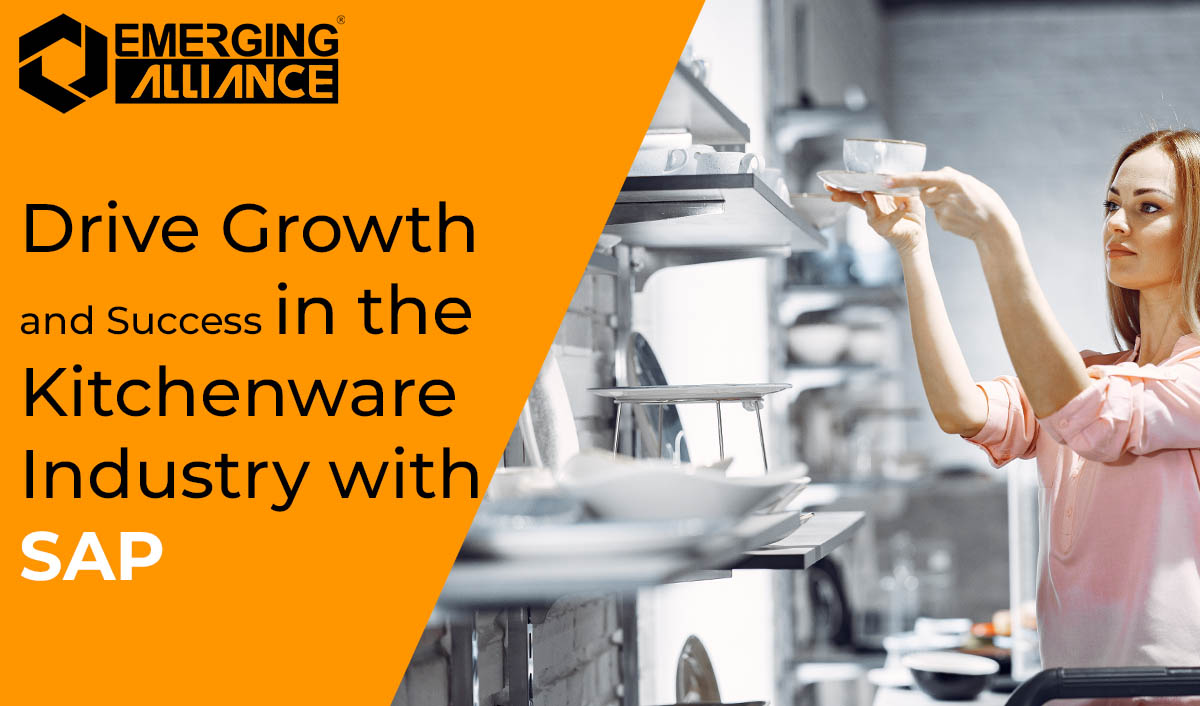
Recipe for Success in the Kitchenware Industry with ERP
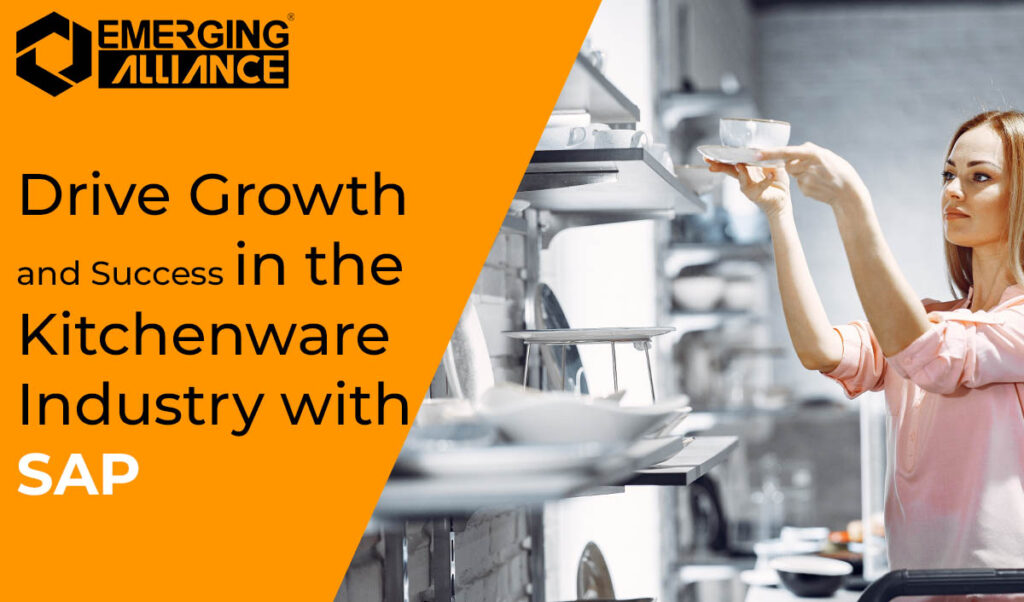
Essential ERP Features for the Kitchenware Industry
In the fast-paced world of kitchenware industries, effective management of resources, inventory, and production processes is crucial for maintaining a competitive edge. Enterprise Resource Planning (ERP) systems have emerged as a powerful tool to streamline operations, improve efficiency, and drive growth. In this blog post, we’ll explore the key features of ERP systems that are specifically designed to meet the unique needs of the kitchenware industry.
Inventory Management in ERP for Kitchenware Industry:
Efficient inventory management is vital for kitchenware manufacturers and distributors. ERP systems provide comprehensive inventory management modules that enable businesses to optimize stock levels, track inventory movements, and automate reordering processes. These features help prevent stock outs, minimize carrying costs, and ensure timely delivery of kitchenware products.
Real-time inventory tracking:
ERP systems provide real-time visibility into inventory levels across multiple warehouses or locations, allowing businesses to make informed decisions about production and distribution.
Batch and lot tracking:
With batch and lot tracking capabilities, kitchenware companies can trace the origin and movement of products throughout the supply chain, ensuring compliance with safety regulations and facilitating efficient recalls, if necessary.
Demand forecasting:
ERP systems utilize advanced forecasting algorithms to predict future demand based on historical data, market trends, and customer behavior. This helps kitchenware businesses optimize their inventory levels and plan production accordingly, reducing wastage and stock imbalances.
Production Planning and Scheduling in ERP for Kitchenware Industry:
Efficient production planning and scheduling are critical to meet customer demand while minimizing costs and lead times. ERP systems offer robust features to optimize production processes in kitchenware industries.
Capacity planning:
ERP systems analyze the available resources, such as labor, machinery, and materials, to determine the optimal production capacity. This helps kitchenware companies balance their workload, avoid bottlenecks, and ensure timely order fulfillment.
Production scheduling:
ERP systems enable businesses to create detailed production schedules, taking into account factors like order priorities, machine availability, and resource constraints. This ensures smooth workflow coordination and helps meet customer delivery expectations.
Shop floor control: ERP systems provide real-time monitoring of production activities on the shop floor, allowing managers to track progress, identify bottlenecks, and make adjustments as needed. This promotes efficient utilization of resources and reduces downtime.
Supply Chain Management:
Effective supply chain management is crucial for kitchenware industries, which often source raw materials from multiple suppliers and distribute products through various channels. ERP systems offer robust supply chain management features to enhance visibility, collaboration, and efficiency.
Supplier management:
ERP systems streamline supplier interactions by automating procurement processes, managing supplier relationships, and monitoring supplier performance. This ensures timely and cost-effective sourcing of raw materials for kitchenware production.
Logistics and distribution:
ERP systems optimize logistics and distribution processes by integrating with shipping carriers, automating order fulfillment, and tracking deliveries in real-time. This allows kitchenware businesses to provide accurate delivery estimates and maintain high customer satisfaction levels.
Demand-driven planning:
ERP systems utilize demand-driven planning methodologies to align supply with customer demand, reducing lead times and inventory holding costs. By synchronizing procurement, production, and distribution activities, kitchenware companies can respond quickly to market fluctuations and changing customer preferences.
Financial Management:
Comprehensive financial management features in ERP systems help kitchenware businesses maintain accurate financial records, improve cost control, and ensure regulatory compliance.
Accounting and bookkeeping:
ERP systems include modules for general ledger, accounts payable, accounts receivable, and financial reporting. This allows kitchenware companies to track expenses, manage cash flow, generate financial statements, and comply with tax regulations.
Costing and pricing:
ERP systems provide tools to accurately calculate the cost of production, considering factors like raw materials, labor, overheads, and machine usage. This helps kitchenware businesses determine optimal pricing strategies and maintain healthy profit margins.
Compliance and reporting:
ERP systems assist in compliance with financial regulations and industry standards. They generate reports and provide audit trails, ensuring transparency and accountability in financial operations.
In the competitive landscape of kitchenware industries, ERP systems play a pivotal role in optimizing operations, improving productivity, and driving growth. By leveraging features such as inventory management, production planning, supply chain management, and financial management, kitchenware businesses can streamline their processes, reduce costs, enhance customer satisfaction, and stay ahead of the competition.
To know more about our products and services, visit us at: https://www.emerging-alliance.com/