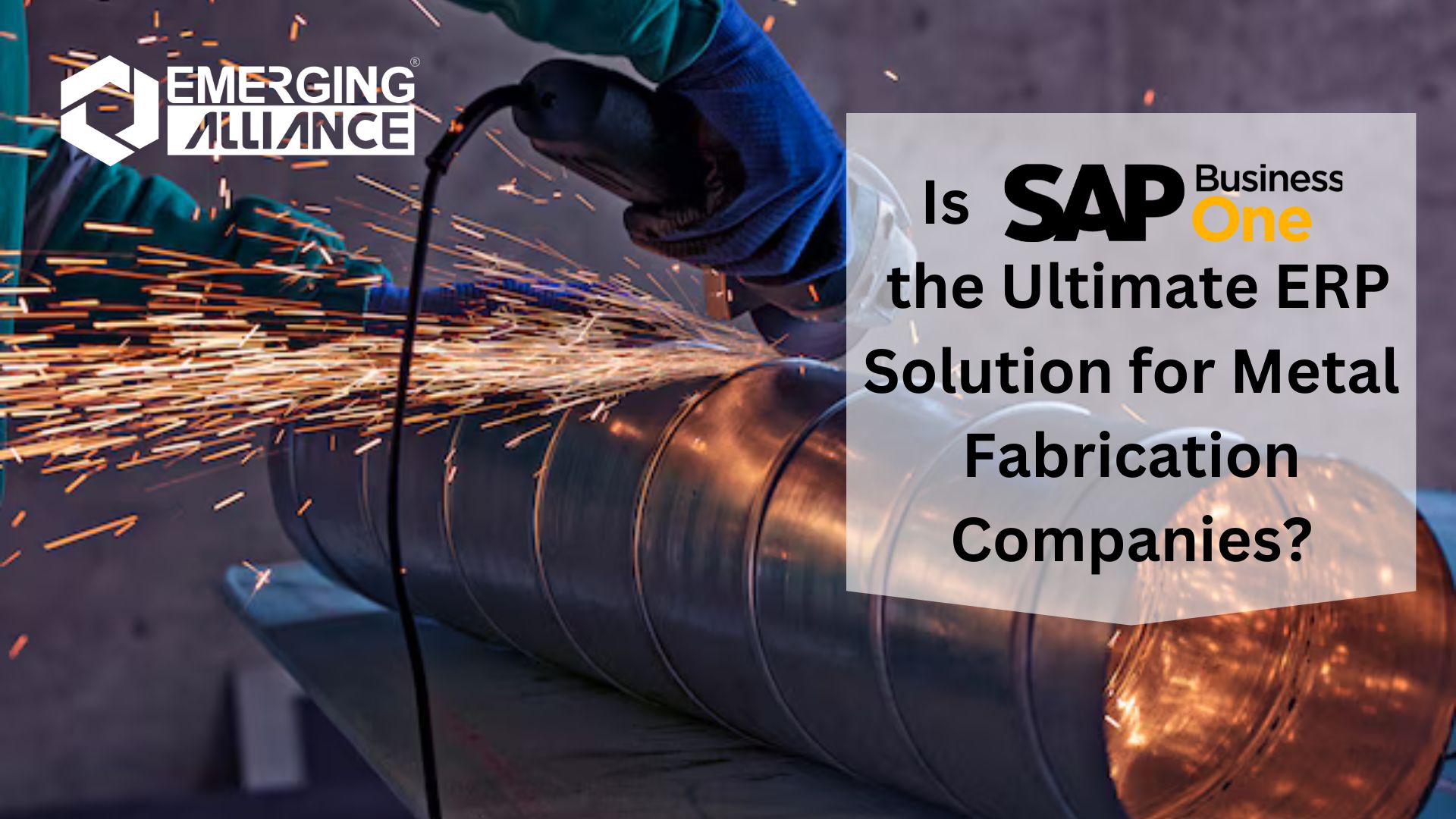
Is SAP Business One the Ultimate ERP Solution for Metal Fabrication Companies?
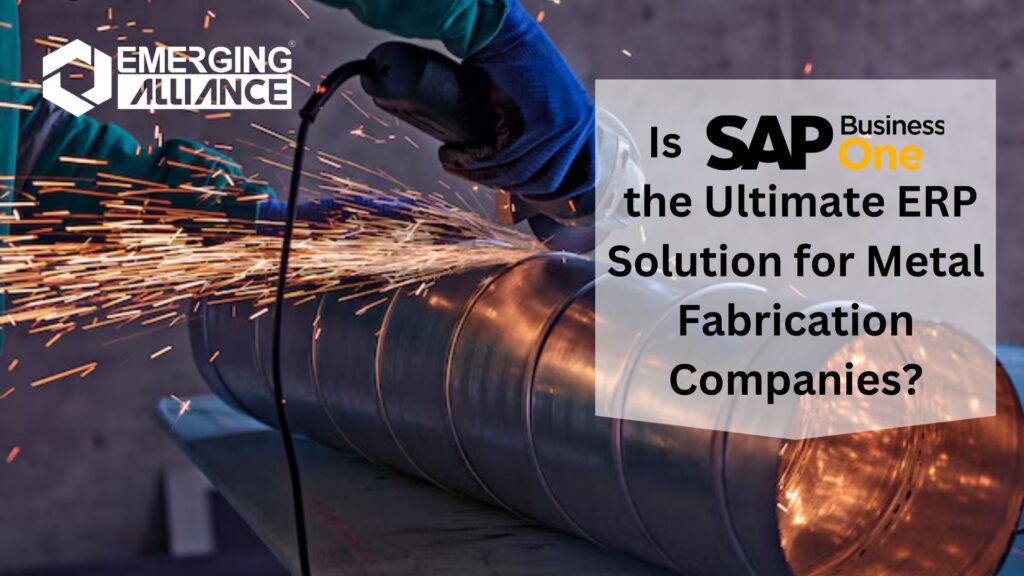
What Makes SAP Business One the Best ERP for Metal Fabrication Operations?
The metal fabrication industry is complex, requiring precision at every stage, from sourcing raw materials to producing finished goods. Managing this intricate process while ensuring scalability and growth can be challenging, especially as the industry faces increasing demand for customization, faster lead times, and cost optimization.
In this article, we’ll explore how SAP Business One (SAP B1), an enterprise resource planning (ERP) solution, can address these challenges and transform metal fabrication production processes. With real-world insights from Raman, an experienced SAP Channel Partner at Emerging Alliance, we’ll dive into the practical features of SAP B1 for metal fabrication companies. Whether you’re in light or heavy fabrication, project-based or turnkey operations, this article will explain how SAP B1 can help optimize your workflows and improve efficiency.
The Metal Fabrication Industry: Challenges and Complexity
The metal fabrication industry involves the transformation of raw metal into finished products through processes like cutting, welding, bending, and assembling. With increasing complexity in production lines, companies often struggle to keep track of various processes and ensure smooth communication across teams. Some of the key challenges in metal fabrication include:
- Material wastage: Managing raw material costs, especially when steel and other metals make up 80% of production costs, is crucial for profitability.
- Inventory management: Maintaining accurate inventory levels and tracking materials through various stages of production.
- Quality control: Ensuring that each part meets strict quality standards through inspection and testing.
- Project-based operations: Managing the unique requirements of project-based fabrication, where each job may require different materials, specifications, and timelines.
For manufacturers facing these challenges, SAP Business One provides a powerful solution to streamline operations and enhance business scalability.
How SAP Business One Can Transform Metal Fabrication Production
SAP Business One offers a range of features tailored to meet the specific needs of metal fabrication companies. Here’s how different aspects of the software can be leveraged for greater efficiency:
1. Item Master and Engineering Change Management (ECM)
In metal fabrication, managing product revisions and maintaining accurate specifications is critical. SAP B1’s Item Master and Engineering Change Management (ECM) features allow businesses to track product revisions and maintain historical records.
- Engineering Change Management helps manufacturers track all revision history, including drawing changes and reasons for revisions. This ensures that only the most up-to-date version of each product is used in production.
2. Auto Weight Calculation for Materials
Another critical feature is the Auto Weight Calculation tool, which helps calculate the weight of materials automatically based on predefined standards. This feature is especially valuable in metal fabrication, where weight plays a significant role in material costs and production efficiency.
3. Incoming Inspection & Quality Control
Quality control is paramount in the metal fabrication industry, and SAP B1 streamlines this process with its Incoming Inspection Addon. When materials arrive, SAP B1 can automatically pull information from purchase orders and load inspection parameters, such as:
- Dimension checks
- Physical and chemical properties
- Visual inspection
Based on the results of the inspection, SAP B1 can automatically move accepted quantities to the accepted warehouse and rejected items to quarantine. Additionally, a Non-Conformance Material Report (NCMR) is generated, alerting quality inspectors to take corrective action. This ensures that only materials that meet quality standards are used in production.
Once the inspection process is complete, SAP B1 also helps create Accounts Payable invoices for accepted materials and credit notes for rejected items, ensuring accurate financial reporting.
4. Single Input, Multiple Output (SIMO) Addon
A core process in metal fabrication is FOP (Flat Plate to Parts), where large metal sheets are cut and shaped into smaller components for assembly. Efficiently managing this process is crucial, as raw materials like steel constitute a significant portion of production costs.
The Single Input, Multiple Output (SIMO) Addon in SAP B1 helps reduce waste and improve material utilization. By receiving a raw steel plate with its unique heat number, SAP B1 tracks the transformation of this plate into smaller parts, managing both primary and scrap materials.
The addon also considers yield optimization, ensuring that the cost of scrap is distributed across the child parts, improving overall material cost management. This is especially useful when paired with nesting software, which further optimizes material usage and reduces waste.
5. Multistage Production Order Addon
Metal fabrication often involves multistage production, where different operations (e.g., cutting, welding, bending) are performed at various stages. Managing multiple Bill of Materials (BOMs) and production orders can be time-consuming and prone to errors.
With SAP B1’s Multistage Production Order Addon, manufacturers can streamline this process by auto-creating production orders based on finished goods (FG). This addon helps manage multilevel BOMs and different operations at each production stage, ensuring that production orders are created in the correct sequence without manual intervention.
6. Project-Based Fabrication Management
For project-based fabrication companies, SAP B1 offers the tools needed to manage unique projects from start to finish. With its ability to track materials, timelines, and costs, SAP B1 provides complete visibility into each project, helping companies stay on track and within budget. The system supports dynamic project management, ensuring all aspects—from procurement to production—are managed in one integrated solution.
Benefits of SAP Business One for Metal Fabrication Companies
- Cost Control: By optimizing material usage, reducing waste, and improving procurement processes, SAP B1 helps manufacturers manage raw material costs effectively.
- Improved Quality: With built-in quality control and inspection features, SAP B1 ensures that only materials meeting strict standards are used in production.
- Operational Efficiency: Automating key processes, such as incoming inspections, production orders, and material tracking, helps reduce manual work, saving time and reducing errors.
- Scalability: SAP B1 can scale with your business, supporting growth as your operations expand, whether you’re dealing with light or heavy fabrication, or handling project-based manufacturing.
- Real-time Data and Reporting: The ERP system provides real-time insights into production, inventory, and financial data, helping decision-makers make informed choices.
The metal fabrication industry faces numerous challenges, from managing complex production processes to ensuring material costs and quality control. SAP Business One is an ideal solution to address these challenges, offering powerful features that streamline operations, reduce waste, and improve overall business performance.
If you’re looking to optimize your metal fabrication operations, SAP Business One can be a game-changer. While this article provides an overview of key features, SAP B1’s capabilities are vast and can be tailored to meet the specific needs of your business. For a deeper dive into how SAP B1 can be implemented for your metal fabrication business, consider scheduling a private consultation with an SAP expert.
Explore more solutions tailored for your industry. Visit our website today: https://www.emerging-alliance.com/
Want to speak to an expert? Fill in the form below, and we will be in touch with you shortly!