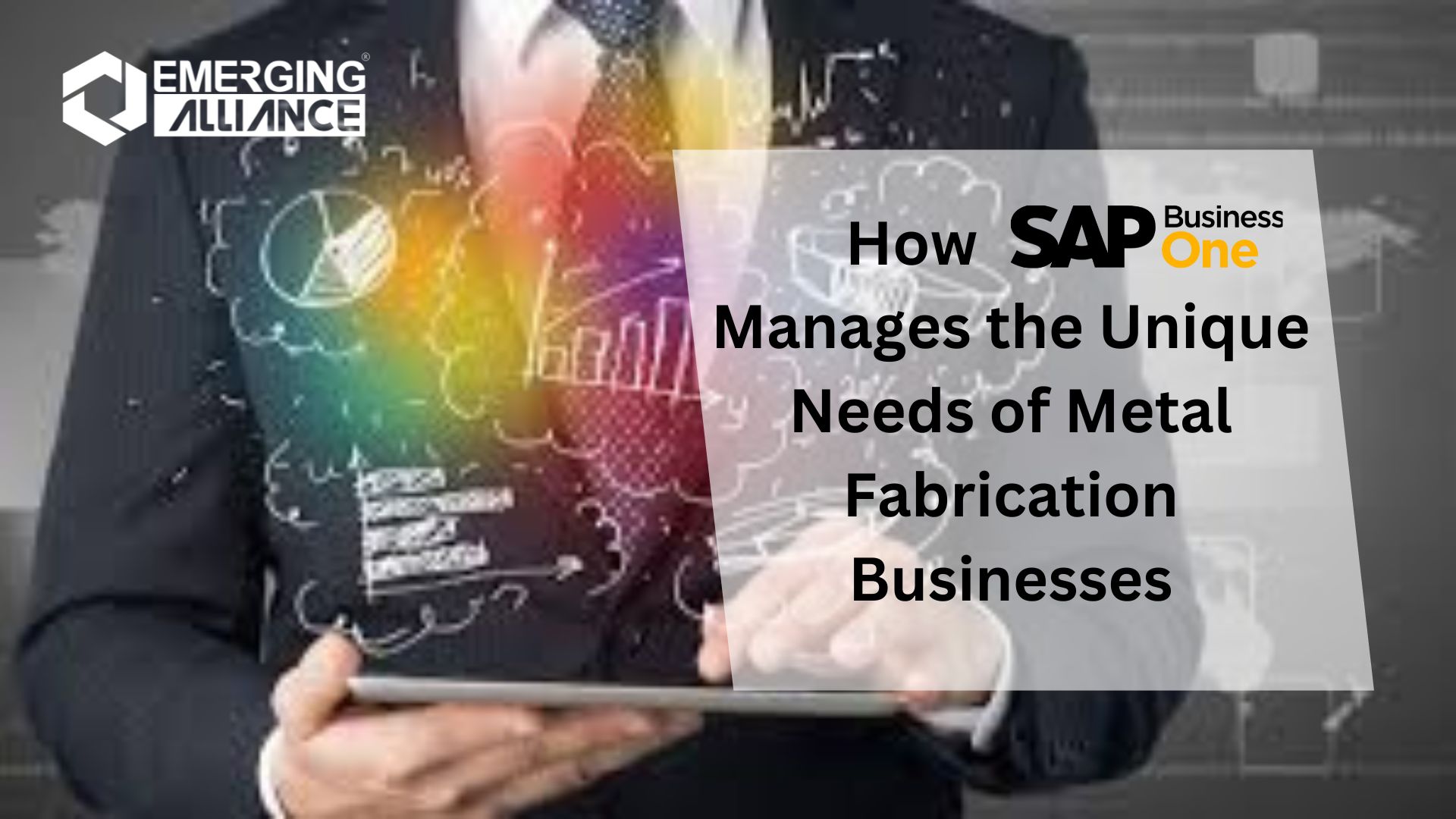
How SAP B1 Manages the Unique Needs of Metal Fabrication Businesses
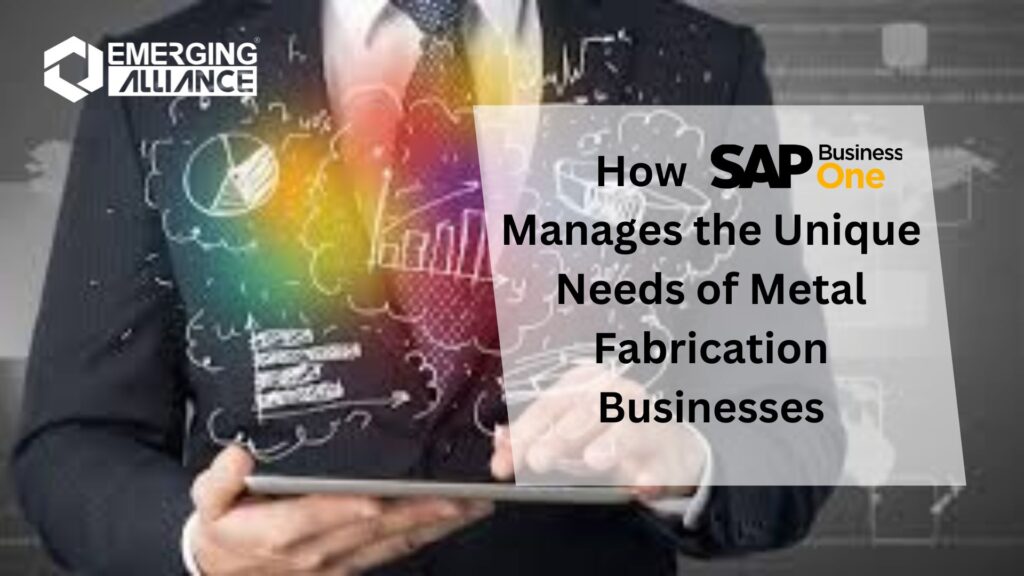
Accelerate Your Metal Fabrication Industry Growth with SAP B1
The metal fabrication industry is a sector marked by complex, multi-stage processes, and requires a high degree of precision and manual intervention at various stages of production. From sourcing materials to managing inventories, overseeing multi-step production processes, handling quality control, and addressing rework, there are many moving parts in a metal fabrication business. This complexity makes the metal fabrication industry one of the most challenging to streamline with software solutions—especially ERP systems like SAP Business One(SAP B1).
In this blog post, we will explore how SAP Business One (SAP B1) can help businesses in the metal fabrication industry tackle common operational challenges and optimize their processes for greater efficiency, accuracy, and scalability. Drawing from the experience of Emerging Alliance, a certified SAP channel partner, this article will delve into key SAP B1 modules and functionalities that can drive growth and operational excellence for fabrication companies.
Challenges in the Metal Fabrication Industry
The metal fabrication industry is inherently complex, and businesses in this field face several unique challenges:
- Manual Intervention: Unlike some industries that can be almost fully automated, metal fabrication often requires manual labor to operate machinery, inspect parts, and address custom customer specifications. This makes it difficult to standardize and automate processes.
- Material Sourcing and Inventory Management: Managing raw materials, tracking inventory levels, and ensuring timely procurement are critical to avoiding production delays or stockouts. Fabrication businesses often need to deal with various suppliers, pricing fluctuations, and long lead times for certain materials.
- Multi-stage Production: A single product may undergo multiple fabrication processes, such as cutting, welding, bending, and finishing. Managing these stages, along with any potential rework, can quickly become overwhelming without the right systems in place.
- Quality Control and Rework: Ensuring that products meet customer specifications and industry standards is a priority. Defects or deviations can lead to rework, which must be tracked meticulously to avoid further inefficiencies.
- Project-based Nature of Business: Many metal fabrication businesses are project-driven, with each order requiring customized workflows and planning. This requires flexibility in the way resources are allocated and tracked.
These challenges make the implementation of an ERP system like SAP Business One a powerful tool for overcoming operational inefficiencies and ensuring long-term growth.
How SAP Business One Can Transform the Metal Fabrication Industry
In my experience working with more than 50 light and heavy fabrication companies, project-based industries, and turnkey solutions, I have seen firsthand how SAP B1 can drive scalability and business growth. In this article, I will share how SAP Business One can be implemented in the metal fabrication industry to streamline operations and enhance efficiency.
The Metal Fabrication Process in SAP B1: Breaking it Down into 3 Major Cycles
SAP Business One helps businesses manage their operations through three main cycles: Order to Cash (O2C), Procure to Pay (P2P), and Plan to Produce (P2P). Let’s explore each cycle in detail.
1. Order to Cash (O2C)
The O2C cycle involves all steps from customer order receipt to payment collection. SAP Business One streamlines this process by providing:
- Customer Drawing Storage: You can store customer drawings, emails, and other communications directly within SAP B1 against a quote or sales order. This helps with easy access and reference throughout the production process.
- Estimation Templates: SAP B1 allows the creation of custom estimation templates, helping businesses generate accurate quotes quickly.
- Quote Management: SAP B1 provides tools for creating and managing quotes, including quote approvals, revisions, and layout options tailored to different customer groups.
- Sales Orders: Once a quote is accepted, SAP B1 links the customer PO to the sales order, setting delivery dates, payment terms, and shipment details. The system even sends order confirmations to the customer automatically.
- Down Payments: The system can generate down payment requests, which are converted into invoices once payment is received. This ensures better cash flow management.
- Invoice Generation: SAP B1 allows for easy conversion of sales orders into invoices, with multiple approval workflows, custom invoice layouts, and built-in profit margin analysis. This includes detailed tracking of order cost vs. production costs, ensuring greater visibility into profitability.
2. Plan to Produce (P2P)
In the fabrication industry, production planning is a critical aspect that requires careful consideration of material availability, machine capacity, and delivery timelines. SAP B1 provides tools to:
- Engineering and BOM Management: If you have a dedicated engineering team, they can create Bills of Materials (BOM) in SAP B1 and upload relevant specification drawings to the item master. This ensures accurate tracking and management of materials.
- Material Requirements Planning (MRP): SAP B1’s MRP functionality helps generate Make and Buy recommendations based on open sales orders, inventory levels, reorder points, and supplier lead times. It helps you plan production and procurement more effectively, ensuring timely material availability.
- Production Orders: You can create production orders based on MRP recommendations and issue material requisition slips for production, controlling both material shortages and excesses.
- Multi-output Production Orders: In the metal fabrication industry, a single sheet or plate may be converted into multiple parts through processes like laser cutting, plasma cutting, or welding. SAP B1 supports this complexity by enabling the creation of multi-output production orders.
- Multi-Stage Production: For complex fabrication jobs that require multiple stages, SAP B1 allows you to create stage-wise production orders with routing sequences. As each stage is completed, the system automatically updates the status and creates the next stage of production, ensuring smooth workflow and proper tracking.
- Quality Control: SAP B1 supports stage-wise quality checks, enabling businesses to record accepted and rejected quantities during production. This helps identify defects early and prevent costly rework later in the process.
3. Procure to Pay (P2P)
Managing the procurement process in the metal fabrication industry is key to maintaining a smooth production flow. SAP B1 offers:
- Purchase Requests (PR) and Purchase Orders (PO): The system enables you to create purchase requests and convert them into purchase orders. It also allows you to collect vendor quotes using the RFQ (Request for Quotation) functionality to compare prices and select the best supplier.
- Goods Receipt and Inspection: When materials are received, SAP B1 helps manage Goods Receipt Purchase Orders (GRPO) and supports inspections to categorize materials as accepted or rejected based on predefined quality standards.
- Landed Costs: For imported materials or complex shipments, SAP B1 allows you to account for landed costs like transportation, customs duties, and handling fees. These costs are then allocated based on factors like weight, quantity, or value, giving you a clearer picture of the true cost of goods.
- Accounts Payable: Once materials are received, the system generates AP invoices, tracks vendor aging, and automatically creates credit notes for any rejected items. This helps with cash flow management and accurate financial reporting.
SAP Business One offers a robust ERP solution tailored to the needs of the metal fabrication industry, from order management and production planning to procurement and financials. By implementing SAP B1, businesses can streamline their processes, reduce inefficiencies, and gain better control over their operations, enabling them to scale and grow in a competitive market.
If you’re interested in learning more about how SAP Business One can benefit your fabrication business, or if you’re facing challenges with your current ERP system, feel free to reach out. We offer customized demos based on your unique business processes and would be happy to discuss how SAP B1 can improve your operations.
For more information on how SAP Business One can transform your business in Metal Fabrication Industry, visit Emerging Alliance.
Want to speak to an expert? Fill in the form below, and we will be in touch with you shortly!