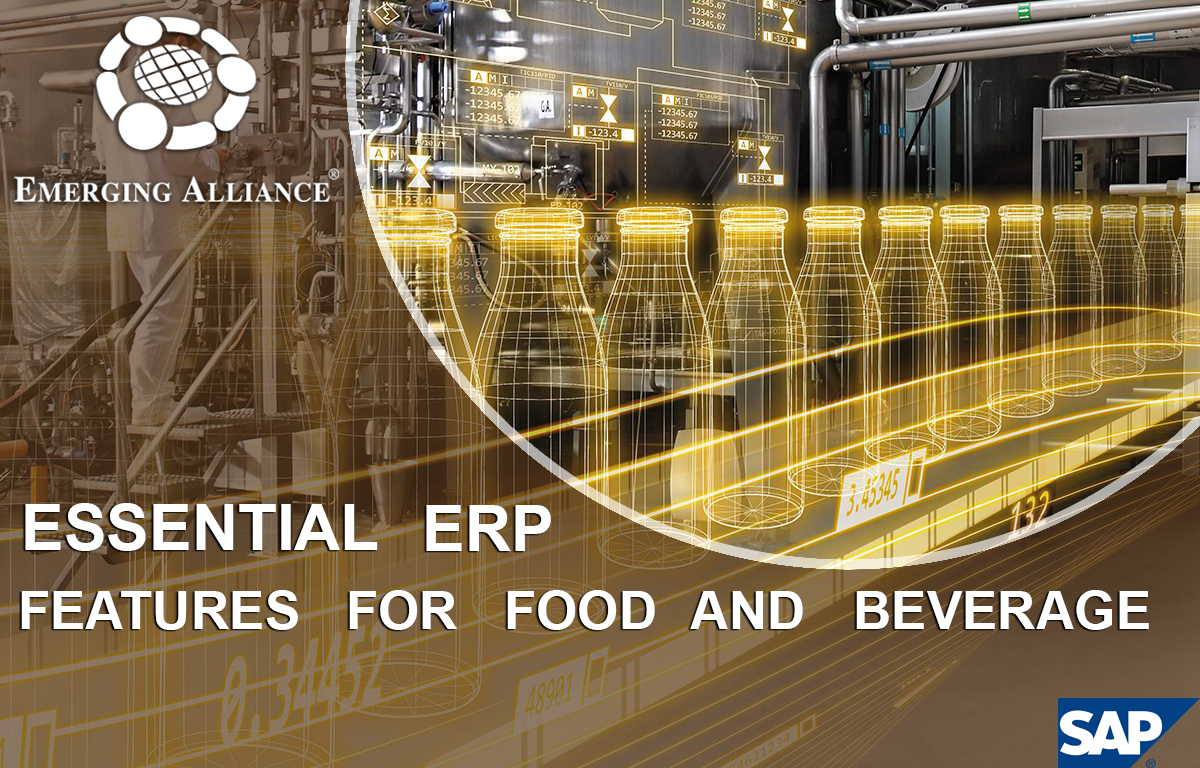
ESSENTIAL ERP FEATURES FOR FOOD AND BEVERAGE
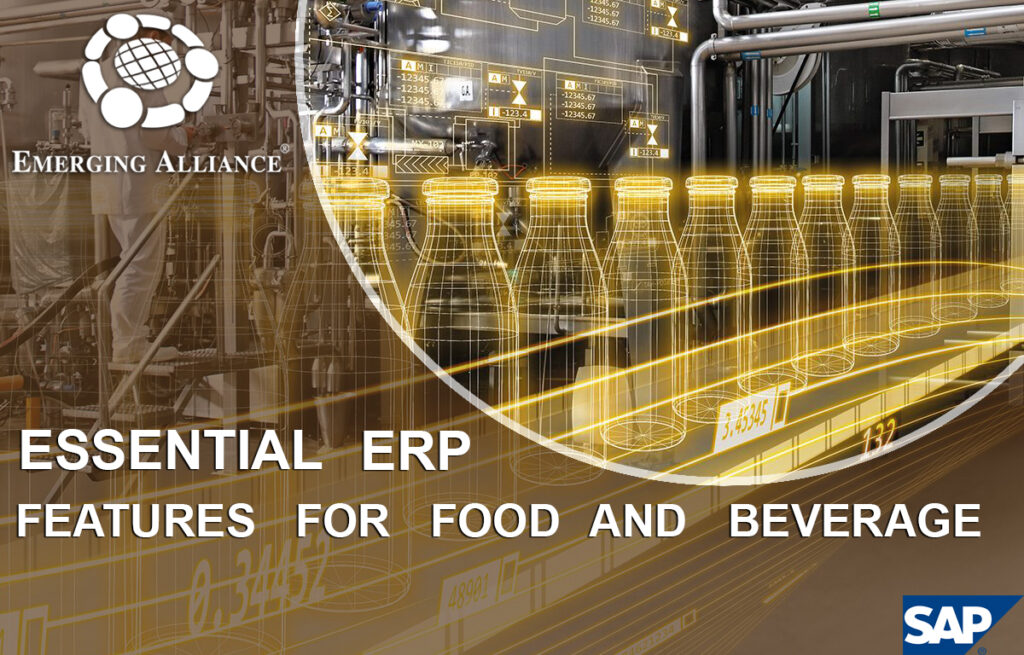
A food and beverage ERP system needs these eight features:
1. TOTAL ONE-UP AND ONE-BACK TRACEABILITY
You need to quickly isolate problems by accurately tracking individual ingredient lots, bins or finished packages as they flow through processing and distribution
SAP gives you instant access to supply chain, production, inspection, genealogy, and usage information.
Eliminate cumbersome manual tracking.
2. SUPERB QUALITY AND SUPPLY CHAIN MANAGEMENT
Product quality depends on visibility. You need a complete, real-time view of production quality across the supply-chain, form supplier operations through to ‘next-step’ customers.
SAP lets you comprehensively track quality and store data for audit.
Innovative tools help you achieve best practices.
3. PREVENTATIVE FOOD SAFETY CAPABILITIES
Only a comprehensive food safety management plan gives you vital control, embracing hazard analysis, critical control points plans process flow charting, statistical process controls and e-signatures.
SAP delivers all this and more.
Move from a reactive to a preventative food safety culture.
4. IN-DEPTH BATCH RECIPE MANAGEMENT
You need to track the extensive data related to batch recipes-from descriptive information and technical properties to quantities, costing information and history.
SAP tracks information for every ingredient in every batch with clear regarding possible allergens.
Rapidly access key data and store it for decades.
5. SMART ELECTRONIC DOCUMENT MANAGEMENT
Creating a streamlined paperless environment lets you fast-track communications with sales and accounting, accelerate operations, increase productivity and reduce human error.
SAP lets you produce and send e-files in any format, with revisions controlled in a smart document management system.
Create a complete product history record.
6. REAL-TIME INVENTORY OPTIMIZATION
Excess inventory and processing delay’s can jeopardize product quality and safety as well as profit. That makes inventory optimization a vital ERP feature.
SAP lets you plan the just-in-time delivery using innovative Materials Requirements Planning (MRP) functionality.
Vital ingredients and raw materials, always at hand.
7. SINGLE-SOURCE SYSTEM INTEGRATION
You need one single-source system that can trace ingredient costs for individual products and product lines in real time-integrated seamlessly with financials, production, quality and inventory
SAP’s unified solution frees data flows between production and accounting: no more tedious or patching or reporting reconciliation.
Gain one version of the truth.
8. INDUSTRY-STANDARD CUSTOMIZABLE BARCODING
Advanced label printing and barcode scanning lets you accurately check quality and cost across you entire product line and ensure that each product contains the right ingredients, added in the right sequence.
SAP’s built-in customizable barcoding features support any format or symbol, meeting GS1 barcode and data standards.
Share information across your supply chain.
Get started today.
Visit: www.emerging-alliance.com