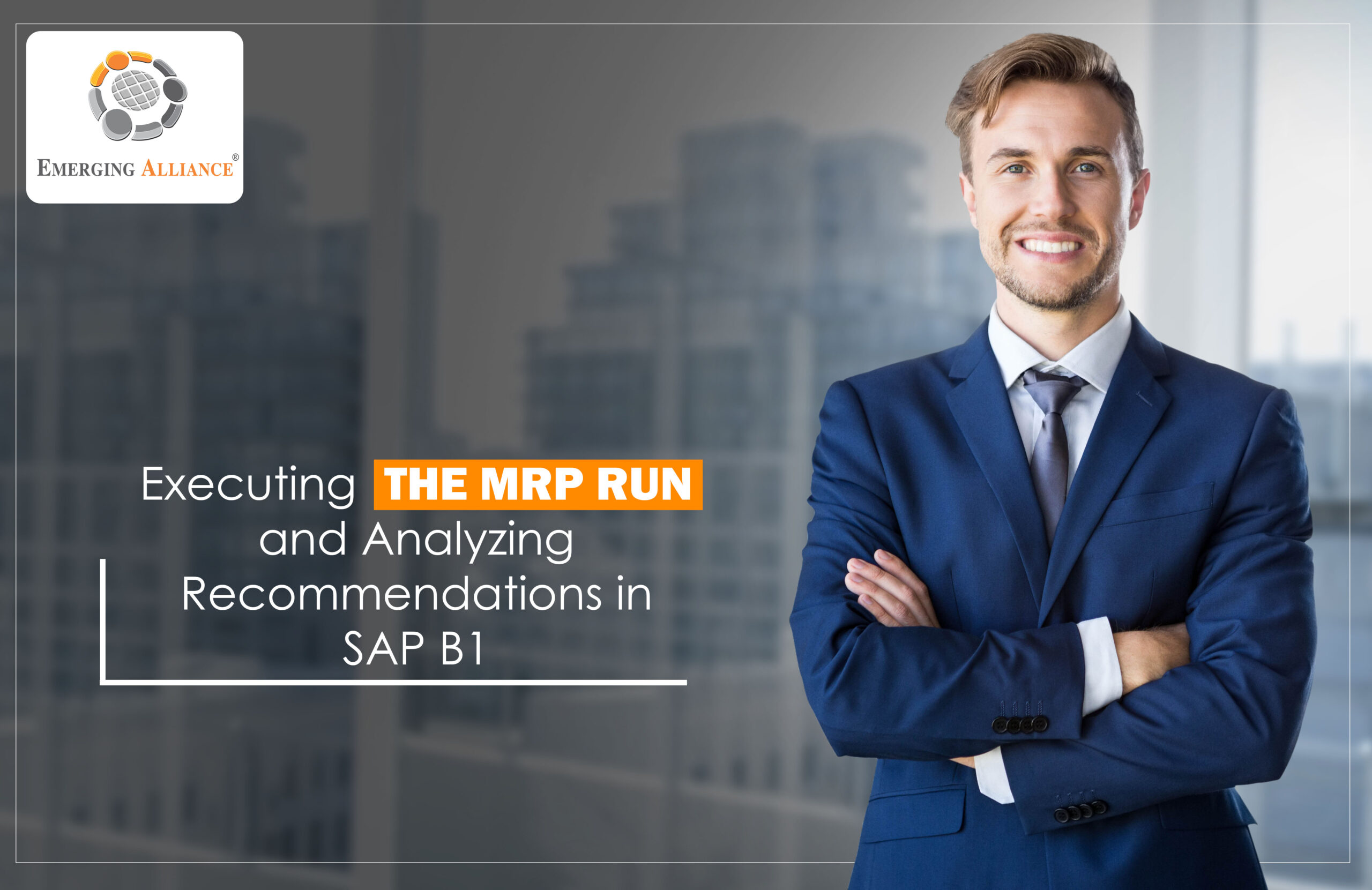
EXECUTING THE MRP RUN AND ANALYZING RECOMMENDATIONS IN SAP B1
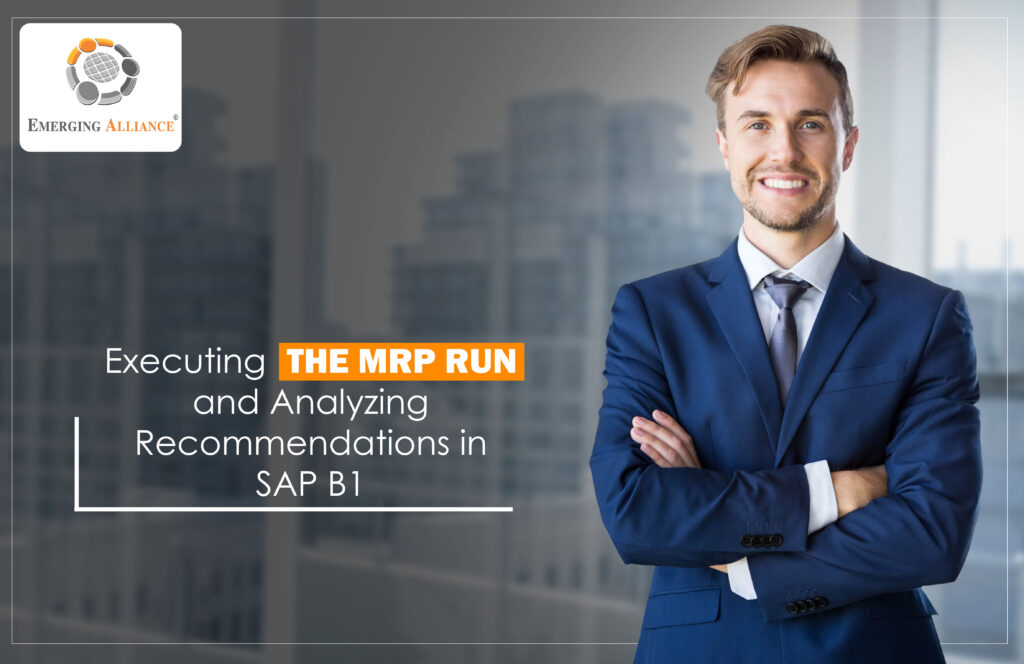
An MRP run is executed by clicking the Run button in the lower right corner on any of the MRP Wizard windows. This triggers the MRP functionality that calculates current inventory and demand for products, reports whether you have enough materials on hand, and makes recommendations about which actions to take to acquire sufficient materials.
How MRP functionality arrived at the results :
- The MRP run created a requirement for the parent item Lexmax printer to fulfil the sales order due on December 09 for 10 units.
- The Lexmax printer has a lead time of 3 days to produce, so the MRP run counts 3 days back from the due date of December 09 to determine the due date of each first-level component needed to build the Lexmax printer. December 7 and 6 are ignored during the count because they fall on the weekend and are considered nonworking days. Therefore, the due date for each first-level component is determined to be December 4.
- The next step is for the MRP run to determine the second-level component requirements. One of the first level components, the power supply assembly, is a sub-assembly with two items; it requires one day for production. In order to have the power supply assembly available on December 4, the AC adaptor and power supply need to be available on December 3.
- Results: The AC adaptor has a two-day lead time, so it is highlighted in red to show it is past due. If today December 1 and the adaptor is needed today, there is no way the item will be in stock in time to fulfil the requirement.
Using the MRP Results window, you can drill down to view the master data for each item by using the orange navigation arrows. In addition, you can examine existing purchase, sales, and production orders; review demand forecasts; and view the inventory levels if you expand the item row in this window.
To see any recommended versions of production orders needed to create the items for the sales order, click the Recommendations tab visible. If you click the Save Recommendations button, you accept and save the recommendations and make them available in the order recommendation report. Remember that saving recommendations does not mean that you have created the production and purchase orders recommended in the report – it simply means that you are saving the recommendations for later use. Read on for more information about this report.
Get started today.
Visit: www.emerging-alliance.com